As digital fabrication reshapes manufacturing, 3D printing is causing a revolution in textile production. This technology enables designers to bypass traditional fabric constraints, creating intricate structures with unprecedented precision and complexity, while furthering environmentally sustainable practices. From adaptive wear to sustainable fashion, this convergence of digital and physical craftsmanship is redefining what's possible in clothing design and production.
What Are 3D Printed Textiles?
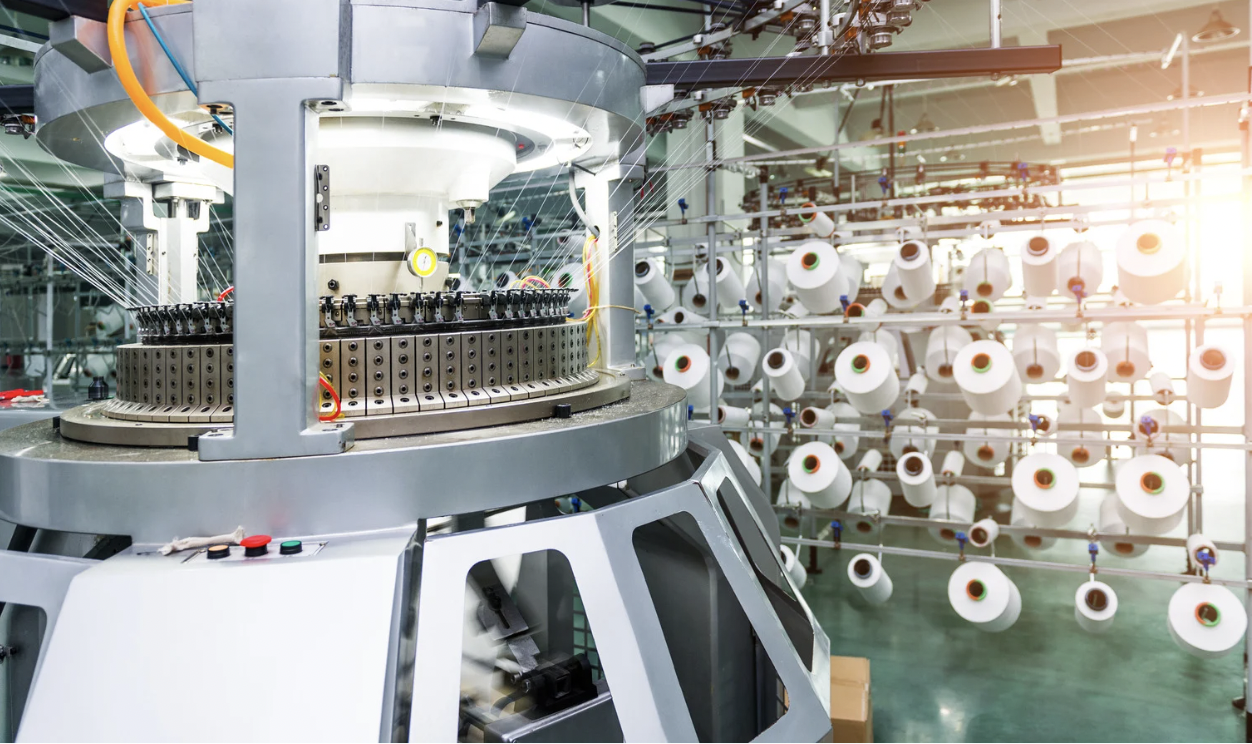
3D printed textiles are an innovative approach to fabric creation that allows designers to overcome traditional manufacturing challenges to produce novel and complex new designs. Unlike conventional weaving or knitting, this process builds flexible structures layer by layer through something called additive manufacturing — the process of creating objects by layering materials, rather than beginning with raw materials and assembling pieces from it together to create a structure. This differentiated process ultimately allows for greater sustainability through reduced textile waste. The journey begins with digital 3D models of the design details, which are then translated into printable STL files.
Digital design tools allow for precise control over every aspect of the textile's structure, from microscopic patterns to macro-level architectures and structural formation. This granular control allows designers to engineer specific properties into different areas of a single piece, such as varying levels of flexibility, breathability, shape or strength.
What Are The Techniques Of 3D Textiles?
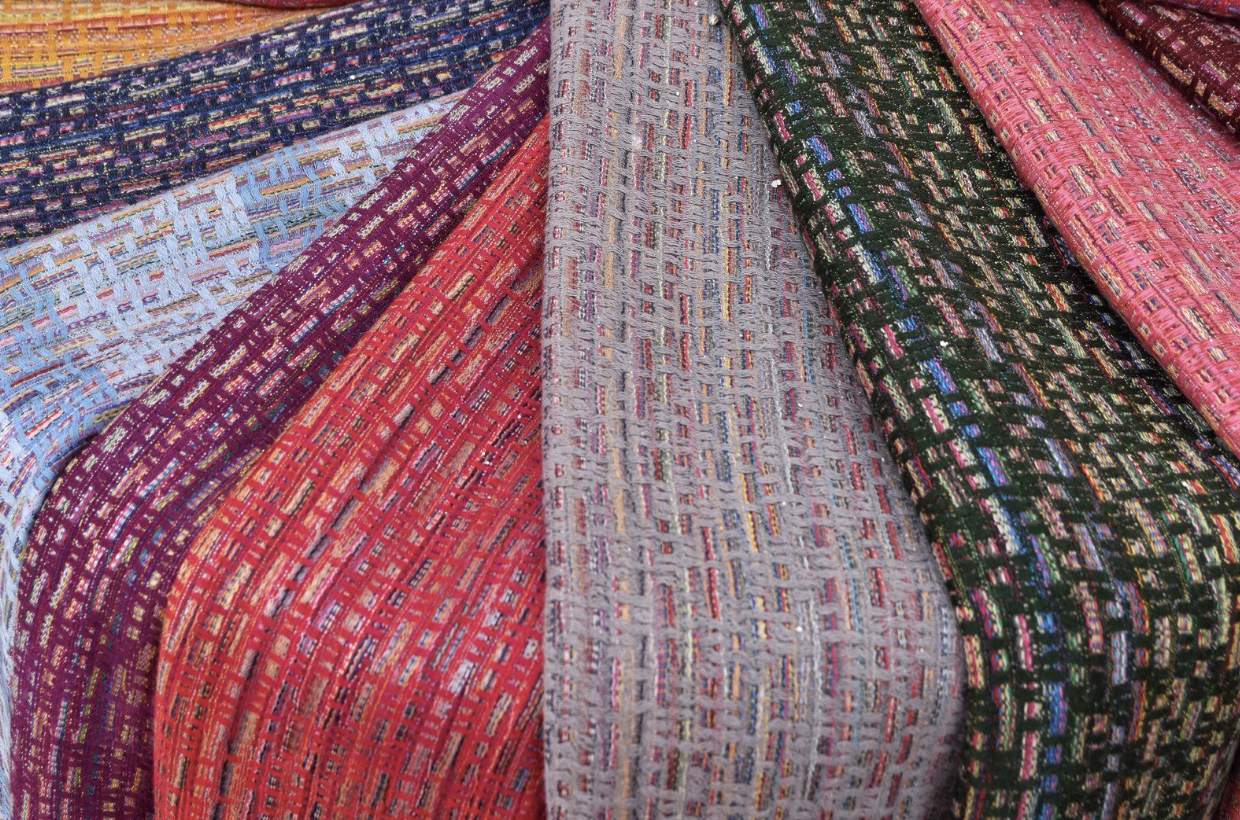
3D textile production encompasses various techniques, each suited to different applications. Fused Deposition Modeling (FDM) allows DIY enthusiasts and small studios to print flexible filaments with an FDM printer directly onto fabrics. This enables seamless integration with textiles, but FDM has lower resolution and slower production speeds than other methods.
Traditional 3D textile techniques, such as weaving, knitting, and braiding, manipulate yarns or fibers to create multi-layered fabric structures.
- 3D weaving interlaces multiple yarn layers to form strong, lightweight textiles used in aerospace, automotive, and protective gear. However, it requires specialized looms and lacks adaptability for intricate designs.
- 3D knitting uses computerized machines to produce seamless, shape-conforming textiles with minimal waste. It is widely used in fashion and sportswear but has limitations in creating rigid structures.
- 3D braiding intertwines yarns to create tubular or complex braided forms. This technique enhances tensile strength and flexibility, making it useful for medical and performance textiles, though less common in fashion.
Additive manufacturing techniques, which build structures layer by layer, mimic fabric-like properties in innovative ways. FDM prints flexible thermoplastic components directly onto textiles. It is cost-effective but has lower resolution and limited durability compared to other methods.
Selective Laser Sintering (SLS) fuses powdered materials with a laser to create flexible, durable lattice textiles. It is widely used in performance apparel but remains expensive and requires post-processing. PolyJet printing uses photopolymer resins to create multi-material, multi-texture prints in a single run. It allows precise control over material properties but is less durable than SLS or fiber-reinforced methods.
Hybrid approaches enhance textile performance. The Continuous Fiber Fabrication (CFF) printing process embeds high-performance fibers like carbon or Kevlar into 3D-printed textiles, increasing strength and durability for aerospace, military, and sportswear applications. Research initiatives such as DefTextiles are advancing smart textiles by integrating conductive materials, enabling responsive fashion and wearable technology. As 3D textile techniques evolve, designers and engineers continue to push the boundaries of performance, sustainability, and aesthetics.
What Types Of Materials Are Commonly Used in 3D Printed Textiles?
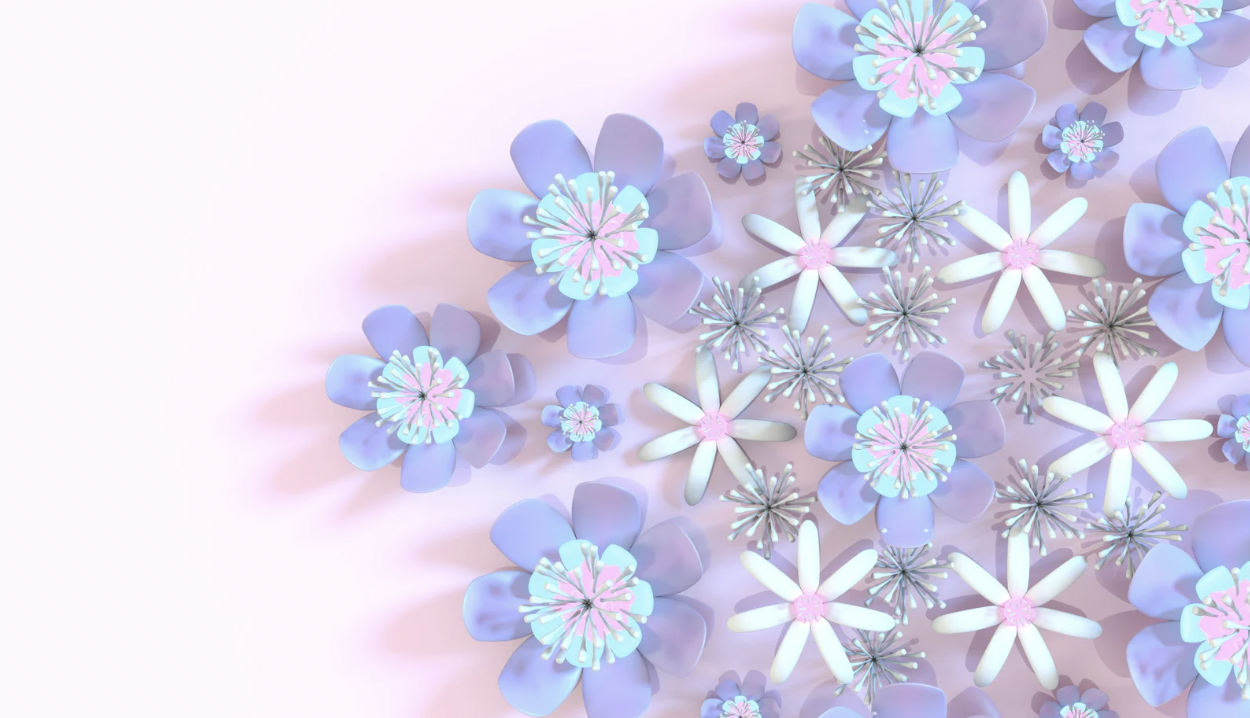
The materials selected are important as they define the characteristics of 3D printed textiles. TPU (Thermoplastic Polyurethane) leads the field for its exceptional flexibility and resilience, while PLA offers an eco-friendly alternative with good printability. Nylon, known for its durability, abrasion resistance, and slight flexibility, is commonly used for functional wearables and high-performance textiles. ABS (Acrylonitrile Butadiene Styrene) provides strong, impact-resistant structures, making it suitable for applications requiring rigidity and toughness while maintaining some degree of flexibility. Advanced polymers and specialized flexible filaments expand the creative possibilities available to designers.
Recent material innovations have introduced properties previously exclusive to traditional textiles. New compounds incorporate shape memory capabilities for adaptive wear, while biomimetic structures enhance performance characteristics. Engineers have developed materials with gradient flexibility within single pieces, enabling temperature-responsive characteristics and moisture-wicking capabilities. Antimicrobial properties can now be integrated directly into the printing material, and biodegradable compositions offer sustainable end-of-life solutions.
The development of these materials requires careful consideration of adhesion properties and structural integrity across multiple layers of printing. Each advancement in material science opens new possibilities for textile design and functionality.
What Are The Advantages of Using 3D Printed Textiles in Fashion Design?
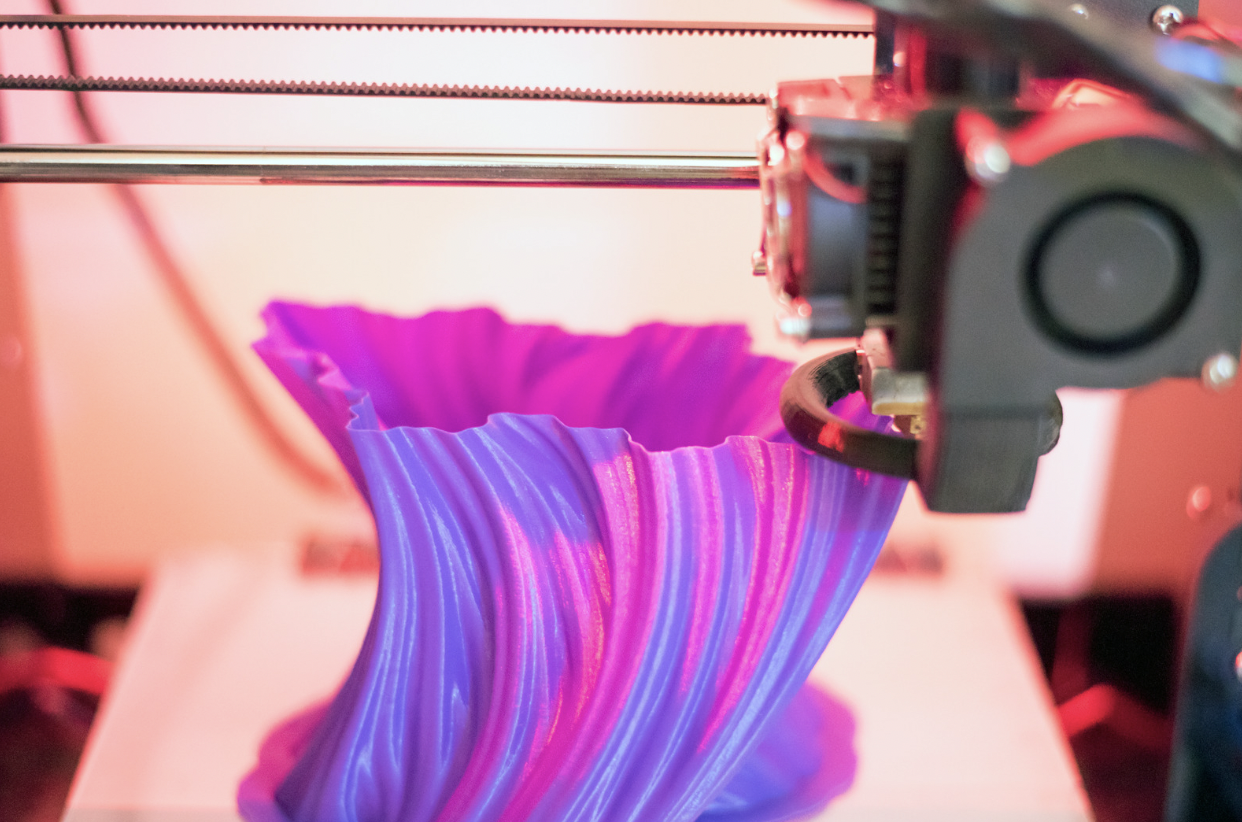
3D printing technology transforms the fashion design process through unprecedented customization capabilities and rapid prototyping potential. Designers in New York and other fashion capitals leverage this technology to compress development cycles from months to days.
The advantages extend throughout the production process. Zero-waste pattern cutting through additive manufacturing significantly reduces material waste. Functional elements can be integrated directly within the textile structure, eliminating the need for separate components. Localized production reduces transportation carbon footprint, while complex geometries impossible with traditional weaving become achievable. On-demand production eliminates excess inventory concerns, and digital archiving of designs facilitates future modifications. The technology also simplifies repair processes and enables more effective end-of-life recycling.
The creation of "smart textiles" represents another significant advancement, incorporating ventilation patterns, flexible joints, and varying densities within a single piece. This capability opens new frontiers in everyday wear, seasonal trends, and specialized applications.
What Are The Current Limitations of 3D Printing Technology in Textile Production?
Despite its transformative potential, several challenges constrain the widespread adoption of 3D-printed textiles. One of the most significant hurdles is the limited range of materials suitable for textiles. Unlike traditional fabrics, which offer diverse fibers with varying textures and properties, most 3D printing materials remain rigid or rubber-like. Even flexible polymers like TPU struggle to replicate the softness, breathability, and fluidity of woven textiles. Additionally, the high costs of industrial-grade printers and specialized materials create financial barriers, making large-scale adoption difficult. The lack of flexibility and comfort in printed fabrics further limits their practical use, as most 3D-printed textiles do not yet offer the stretch, drape, and tactile qualities needed for comfortable wear. Layered structures often result in stiffness, restricting movement and reducing overall wearability.
Scalability remains another major challenge. Unlike traditional textile manufacturing, which efficiently produces fabrics in bulk, 3D printing is still a slow and resource-intensive process, making it impractical for mass-market production. Durability and wearability also present concerns, as many printed materials degrade more quickly than woven or knitted textiles when exposed to washing, repeated wear, or environmental factors. Additionally, slow production speeds further hinder adoption, as each layer must be meticulously built, making it difficult to meet high-volume demand efficiently. These limitations, combined with high energy consumption and the need for specialized technical expertise, illustrate the significant hurdles that must be overcome before 3D printing can fully integrate into mainstream fashion production.
FAQ
How Expensive Is The 3D Printer?
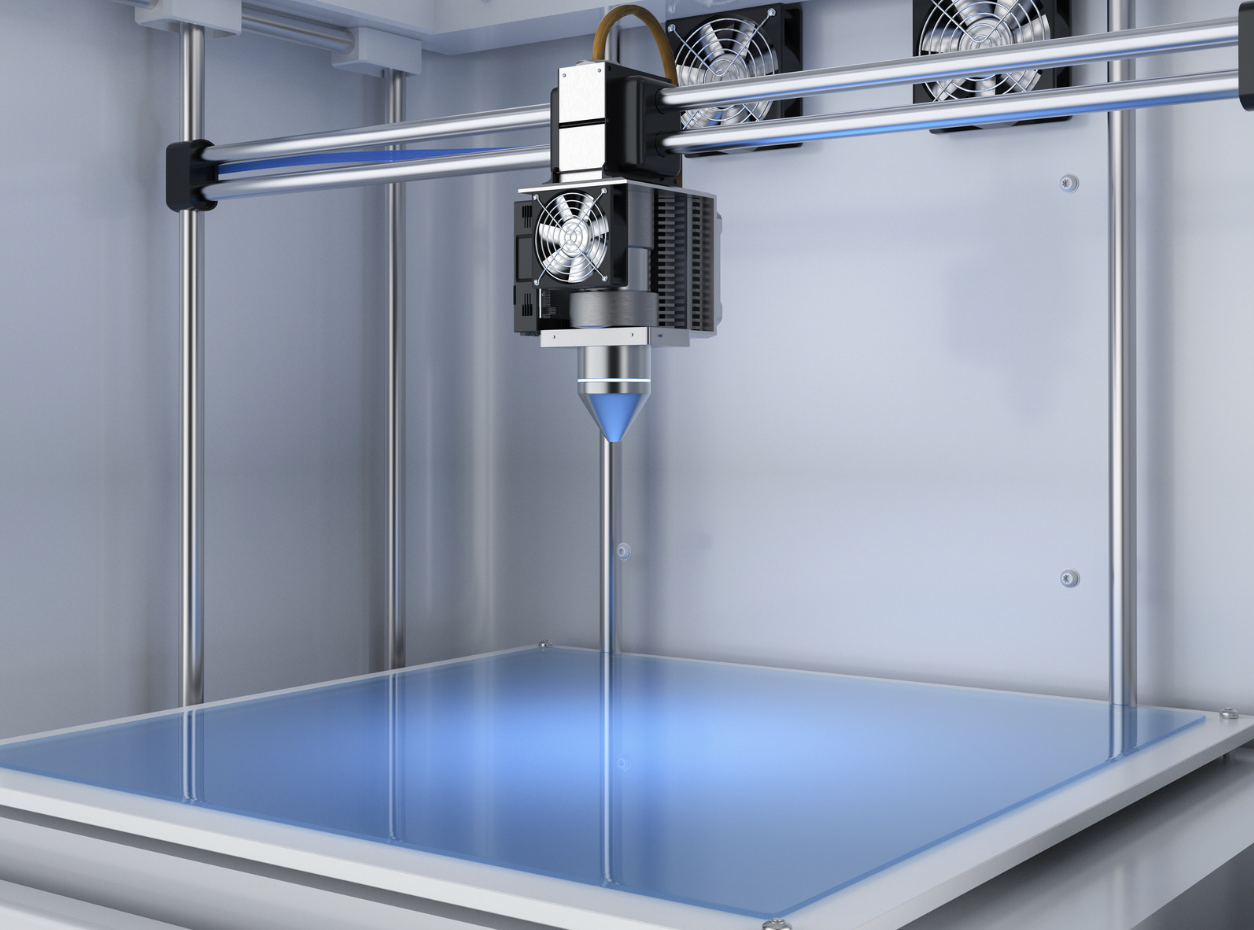
The cost spectrum for 3D printers ranges from entry-level machines ($200-$500) to industrial systems exceeding $100,000. The total investment includes ongoing expenses for materials, maintenance, software licenses, and operator training. The choice depends on production requirements, quality standards, and output volume needs.
How Can 3D Printing Help the Textile Industry?
3D printing revolutionizes textile production and pattern development through digital customization, waste reduction, and rapid prototyping capabilities. It enables the creation of previously impossible structures while supporting sustainable, on-demand manufacturing models. This technology particularly excels in specialized applications where traditional methods fall short.
What Is The Best Fabric To 3D Print On?
Success in direct-to-textile printing depends on substrate selection. Stable materials like polyester-cotton blends and technical meshes provide optimal foundations. The base fabric must be able to withstand printing temperatures while maintaining dimensional stability. Surface treatment and material compatibility testing are essential for achieving reliable results.
Join the 3D Textile Revolution! The Pattern Cloud connects you with leading studios pioneering 3D printed textiles, offering access to cutting-edge technologies and expert collaborators. Elevate your designs with sustainable, customized innovations and explore the future of fashion.